Quality Advisor Blog
Influential Voices of Quality Blogger
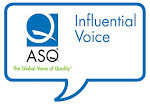
ASQ Fellow, Don Brecken, is part of the ASQ Influential Voices program. While he receives an honorarium from ASQ for his commitment, the thoughts and opinions expressed in the blogs below are his own.
ASQ Influential Voices Contribution: Making a Quality/C-Suite Connection
West Michigan's Most Influential Quality Professional
ASQ Influential Voices Contribution: Quality in a Rapidly Changing World
Change is the only constant. Greek philosopher Heraclitus (c.535 BC – 475 BC) is credited with this universal doctrine which tells us nothing endures but change. Isaac Asimov, prolific author and humorist, states “The only constant is change, continuing change, inevitable change, that is the dominant factor in society today. No sensible decision can be made any longer without taking into account not only the world as it is but the world as it will be.” If change is inevitable, how must we deal with it?
Quick, simple, and agile. Nothing should be so etched in stone that it cannot be changed. Think about the long-term implications of today’s decisions. What will happen if conditions change? Is your solution one that will stand the test of time or will you eventually have to go back to the drawing board? Can better, more long-lasting decisions be made? Quality professionals should consider the big picture and long-term implications of their decisions.
Bend, don’t break! When faced with pressures to change, quality professionals must find ways to keep up with the change while remaining true to their principles. I recall a major product launch where a “rush to market” approach taken by top management caused an entire team of quality professionals to compromise their principles. Several very important quality-related tollgates in the product development process were skipped. These quality professionals were forced to bend to the point of breaking. And break they did; they compromised their principles. When the product reached the customer for assembly in the field, various components did not fit together.
Haste makes waste. In the example above, hurrying and hastily-made decisions caused the company to spend millions of dollars for product redesign and retrofit. The pressures to hurry can sometimes be great. Quality professionals need to be agile and willing to bend when faced with these pressures to change; important principles, however, should not be compromised. Quality professionals need to stress that “hurry-up can wait” and “slow can sometimes be fast.” We see examples of this every day where we don’t have time to do it right the first time but we always find the time to do it again.
It’s all relative. I left one industry for a job in a completely different industry a few years back and the hiring manager warned me about the fast-paced nature of his industry. Nothing could be further from the truth from my perspective. In the make-to-order industry, I came from we dealt with thousands and thousands of pieces in various stages of production. You could literally stand in one spot in any of our facilities and watch production flow all around you. In this new, one-off production environment, however, you can watch a job sitting on a machine for hours or on the shop floor, sometimes for days, waiting to be processed further. This is hardly a fast-paced environment from my perspective and far from the fast pace environment in Paul Borawski’s consumer electronic product example.
Where to Begin When Starting Over?
No longer does the burden for the QMS fall on just a couple dedicated employees. The managers who were not previously engaged in the QMS are now process owners. Process owners are responsible to establish, document, and maintain their respective processes and work to continually improve its effectiveness and interaction with other processes.
This is where we begin. Then to sustain these changes we audit. We audit the process to ensure each has an approach that is deployed where needed, delivers intended results, and is continually improved. We also audit process results to ensure the process has key performance indicators, tracked levels of performance, and positive trends.
This is where we begin when we must start from scratch. Then once the leadership fully embraces and masters the process approach by managing the organization as a system of interrelated processes the rest of the QMS requirements are relatively easy to deploy.
Holistic Quality Improvement: Everything By Process
Those of us fortunate enough to be employed own the process of getting up and making our way to work. We have worked this process over and over and found ways to eliminate those obvious sources of process variation. We have it figured out. We take it for granted since it's not all that complex and we get repeatable results, day after day.
Processes internal to organizations, however, can be quite complex. No matter the size or type, whether it produces product or services, all organizations are systems of interrelated processes where the output of one process invariably becomes the input to another process. And like the process of getting to work in the morning that we each own, processes internal to organizations also have owners.
These owners are responsible for managing, monitoring, measuring, and continually improving their processes.
This focus on process improvement is a holistic approach to improving organizations. Holistic improvement requires a wide variety of tools. It may also require that these tools be used in new or different ways. I have improved organizations through the practical application and use of the organization's quality policy, quality objectives, audit results, analysis of data, corrective and preventive action, and management review. I personalize this improvement approach with a proprietary mix of simple quality tools, Six-Sigma concepts, and Baldrige Criteria.
Treating the whole organization with a holistic approach to quality improvement will increase the likelihood of success and long-lasting results. Surgically improving the organization here and there will likely result in failure.
ASQ Influential Voices Contribution: Give Yourself a Raise!
Looking Back at 2012
It can be difficult to recall all the positive things you did over the last year to increase your value to your organization. Personally, I do a horrible job of keeping track of the many positive things I do to increase my value to the organization. Like most quality practitioners, I don’t spend enough time making the case for “me.” In general, we are humble servants who would rather focus our attention on how “we as a team” made a difference and how “what we did” adds value. We seldom take enough credit for our own accomplishments. We don’t bang our own drum enough with regard to our own personal contributions and, consequently, we often are shorted when it comes to raises and advancement.
Rather Underemployed than Unemployed
There are times when we must be content with what we have and even settle for less. Being underemployed is far better than the alternative: being unemployed. The 2012 Salary Survey seems to support the fact that we quality professionals, on average, earned less last year than in previous years. It’s currently a buyers market; that is, there seems to be more unemployed and/or underemployed quality professionals out there than in previous years and personnel managers are able to hire a lot of professionals for relatively little money. In these difficult times, when it seems we must accept lesser employment or otherwise be unemployed, we may be overlooking our options. Many of us absolutely do have other options.
Give Yourself a Raise
One such option is to give yourself a raise. Unless you are self-employed, your employer has control over the paycheck you earn at your 9 to 5 job. However, you have control over your free time and how it is spent. You can sit on your couch after work and wish your organization would recognize your contribution one day and give you a raise or you can use this time to give yourself a raise. As quality professionals, we have other options. We can teach a course in quality at our local community college. We can hold an occasional seminar on our favorite quality tool. These and other means of generating income are great ways we quality professionals can give ourselves a raise. Do we ask for a raise from our employer when money is tight and our case may be weak or do we look at creative ways of giving ourselves a raise?
ASQ Influential Voices Contribution: Definition of Quality
How My Students Define Quality
Week 2 of this semester I asked my MGMT 370 Quality/Operations Management students to take a stab at defining quality. Seven groups with 5 students each put their heads together to craft their own definition of quality. Students were allowed to reference other definitions but if their definition turned out to be even loosely based on someone else’s they were required to credit the source.
Below are my student’s submissions. Some liberty was taken with regard to editing their statements, but not much. Any resemblance to someone else’s definition of quality is purely happenstance.- Quality is meeting and/or exceeding customer expectations of form, function, and service. Quality is the voice [an expression or outcome] of a company which can be measured by applying statistical tools.
- Quality is a degree of excellence of product or service when compared to the competition and standards.
- Quality is the total best cost for the best product; you get what you pay for! Quality is meeting and exceeding customer expectations and an ongoing process of building and sustaining relationships by anticipating needs. Quality varies from company to company and within companies.
- Quality means a product or service has exceeded standards of what is expected in an industry; accepted/acceptable by the customer. A reputation for quality sets a standard for what is expected. Quality results from tested, processes of research and development. Quality continually improves through change. Quality sets you apart from your competitors, has appeal, is durable, and meets standards set by industries.
- Quality is subjective, a level of excellence, is reliable, maintainable or sustainable, and is durable.
- Quality means getting what you pay for as a consumer and creating a product that lasts as a producer. It is a Utopian idea of how a product is made or service produced by obtaining the finest ingredients to produce the highest quality product or service. Quality is a comparative measure by which other products or services are judged. Invoking the perception of quality; the gold standard; the Cadillac of…
- Quality has two different prongs: consumer quality and producer quality. Consumer quality is a subjective perception of quality surpassing that of the competitors. Producer quality is the measurable aspects working toward a final predetermined outcome.
- Quality is the standard of something as measured against other things of a similar kind. In order to know something is quality we need to have a standard of something to measure it against. Everything has a different standard of quality so that is why we need different standards for which to make comparisons.
How My ASQ Student Branch Members Define Quality
I challenged our ASQ student branch members at Ferris State University – Grand Rapids to take a stab at defining Quality. Find our student branch on Facebook at https://www.facebook.com/#!/groups/asqrsofsu/.To jump-start the topic I asked: Is Quality defined as Function and fit? Customer satisfaction? Compliance with requirements? Meeting customer specifications? Producing parts within tolerance? Defect-free? On-time delivery of product or services? Or is quality more of an abstract such as Luxury? A gut feeling? Or the "wow" factor? A couple of student branch members' responses follow:
- Quality is all of the above. There is a requirement from the customer and without satisfaction, the customer will go somewhere else. I work with Ford components for the F150, 250, and 350, one of the earlier customers changed the machine without Ford's knowledge, which then created a defect on our end. It took two months to discover where the problem stemmed from, and a lot of money involved. Therefore production, meeting requirements, defect-free, and on-time delivery are all a part of quality.
- I perceive Quality as the end user’s (consumer) perception of the goods. Fit/function requirements, design specifications, and customer satisfaction data points (on-time delivery, defect-free) are all driven back from there. Even if you produce goods to specification for your “customer” and they are satisfied, if the end-user or consumer does not like it, quality is still perceived as low. This is where the emphasis within manufacturing to watch JD Powers initial quality ratings and consumer satisfaction surveys come from. These items will drive tighter tolerances or new designs in order for that customer to stay in front of their competition to catch the highest share of the market in quality. However, the inverse of this, too tight of customer satisfaction requirements, drives unnecessary cost into a product that the end user would never perceive as being low in quality. Voice of the end consumer is key.
My Single Declarative Definition of Quality
Like beauty, quality is in the eye of the beholder. Maybe more accurately, the “definition of quality” is in the eye of the beholder. Most of us, in my opinion, recognize quality when we experience it. We know what “Wows!” us. Below is my single, declarative definition of quality.
- Quality is an abstract state of excellence or goodness characterized by the extent to which discriminating consumers are satisfied with the particular product and/or service consumed.
West Michigan's Most Influential Quality Professionals: A Panel Discussion on Contemporary Issues in Quality
How My Students Define Quality
Correlation Does Not Equal Causation
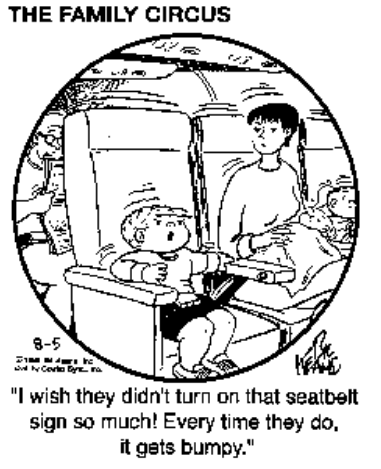
Water: Does Quality Really Matter?
West Michigan's Most Influential Quality Professionals: A Panel Discussion on Contemporary Issues in Quality
Systems Theory Practical Application
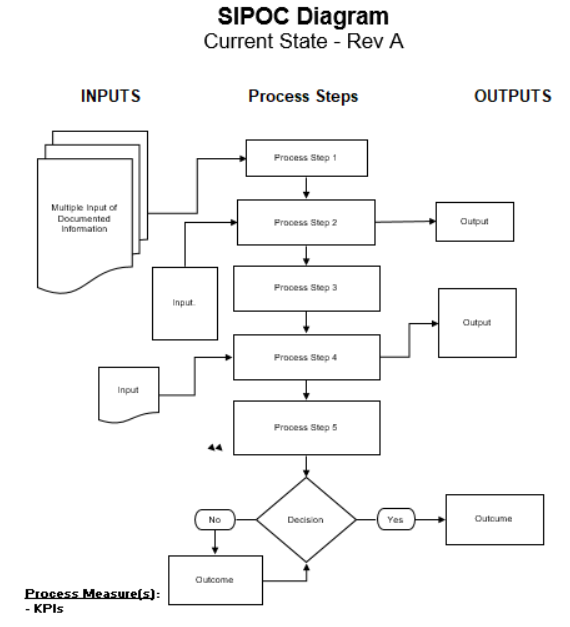